
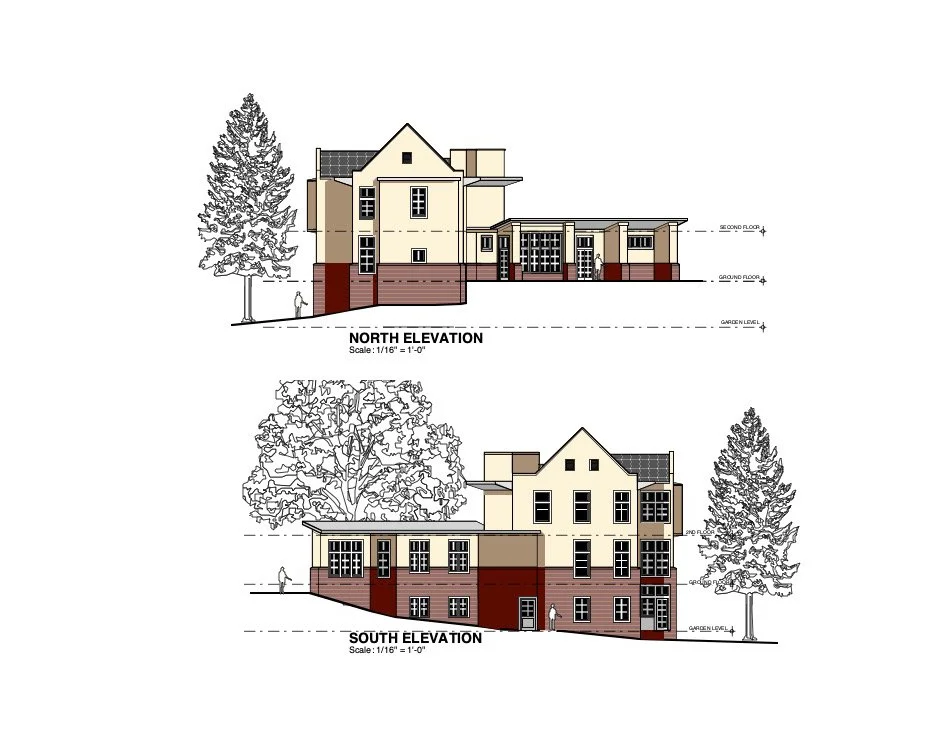

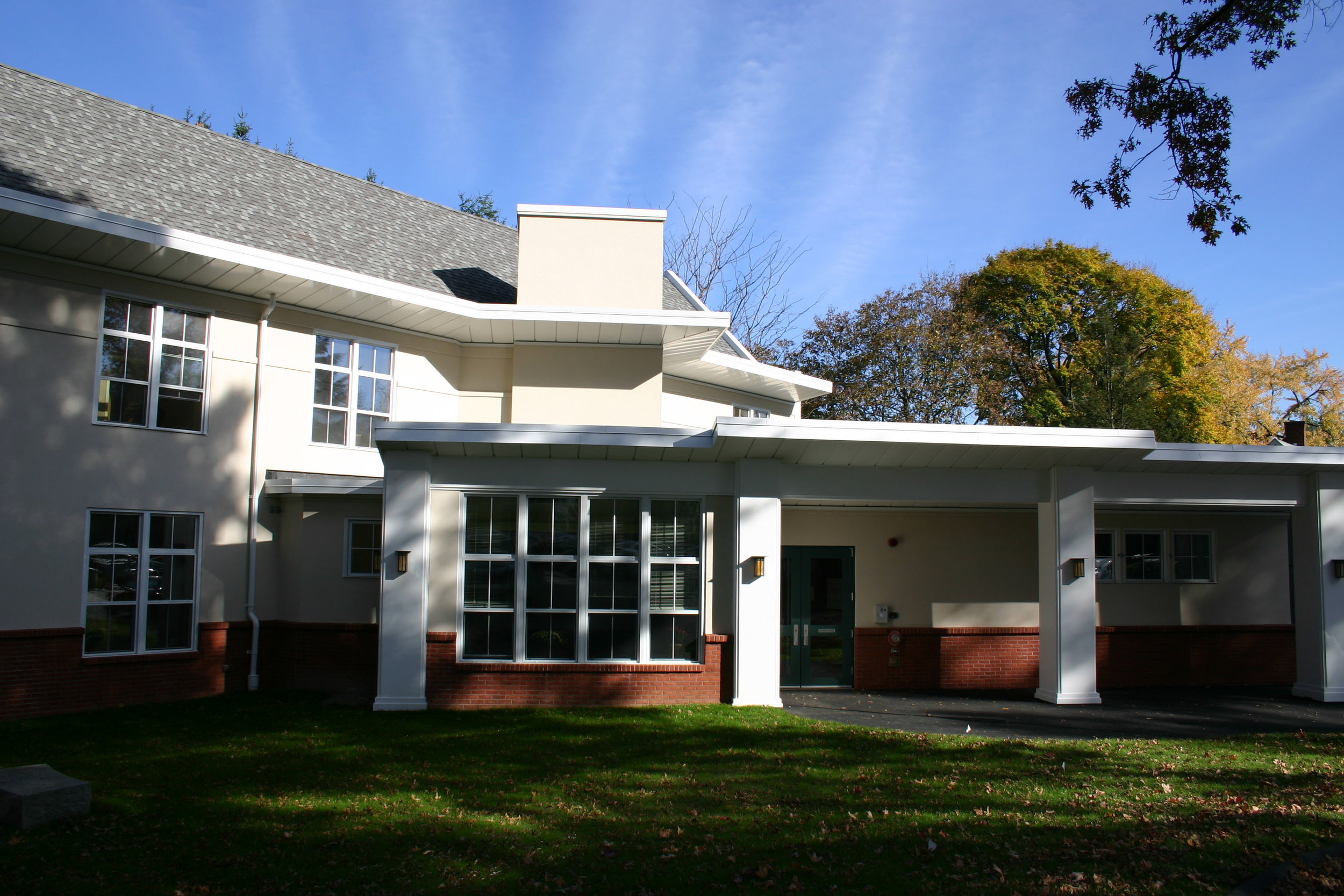
The Conway House sits back from the road close to downtown Northampton, protected from traffic and surrounded by trees. This new construction was built to provide apartments for non-traditional Smith College students, some with families. The three story, 13,000 square foot building has ten two bedroom apartments, one of which is fully accessible, and several common areas for laundry, storage and socializing.
The building is super-insulated and has large insulated triple-glazed windows that allow for plentiful daylighting but limit energy loss. Interior finishes were chosen for their natural durability, beauty and environmental integrity - natural resilient flooring, Green Seal certified carpets and low VOC paints, adhesives, and composite materials. Additionally, the building used an energy recovery ventilator to conserve energy as the fan ventilates the house.
Sustainable Features:
Energy Efficiency:
Very high insulation values – R-48 & R-56 Walls, R-70 ceiling (attic)
Very high performance windows – all fiberglass construction, triple pane glass (R-7)
Air tight detailing used extensively (Note: the building was “blower door tested” by Energy Star technicians reaching a level of tightness 3 times lower than minimum)
Constant volume ventilation with energy recovery has been installed to maintain a fresh air supply. (This system continuously exhausts air from the bathrooms while fresh air is supplied to the corridors. Heat & moisture energy is recovered with equipment installed in the attic).
Air conditioners, refrigerators and dishwashers are Energy Star rated.
All lighting is compact fluorescent with a very low Watt to lumen ratio. The lamps were provided by the Energy Star program.
Digital controls in each room control the heating system.
Heating is provided by two, wall mounted gas fired boilers located in the lower level mechanical room. (They are modulating boilers, digitally controlled, that will produce heat based on outside air temperature and domestic hot water demand)
Materials:
Wall insulation is made of expanded polystyrene. (The same material disposable coffee cups are made of).
Attic insulation is blown cellulose treated with boric acid.
All paints used are low VOC (volatile organic compound) or no VOC.
Marmoleum floors were installed in kitchens, baths and corridors (no vinyl’s used) Marmoleum is made from primarily natural raw materials; linseed oil, rosins, and wood flour, calendered (pressed) onto a natural jute backing.
Rubber base was used in the kitchen and bathroom not vinyl.
Carpeting is made of nylon, constructed and installed using very low VOC glues.
A few other notes:
The ceilings were raised higher than most residential buildings to accommodate a third sash. With taller windows, natural light can penetrate deeper into the rooms. Mini blinds were installed for best control of natural light and privacy.
The buildings heating system is designed to accommodate the addition of solar thermal panels in the future.